Engel Highlights Automotive Molding Applications at Chinaplas
Mobility is a core market segment for the Austrian machine builder and its production assets in China and beyond.
April 29, 2024
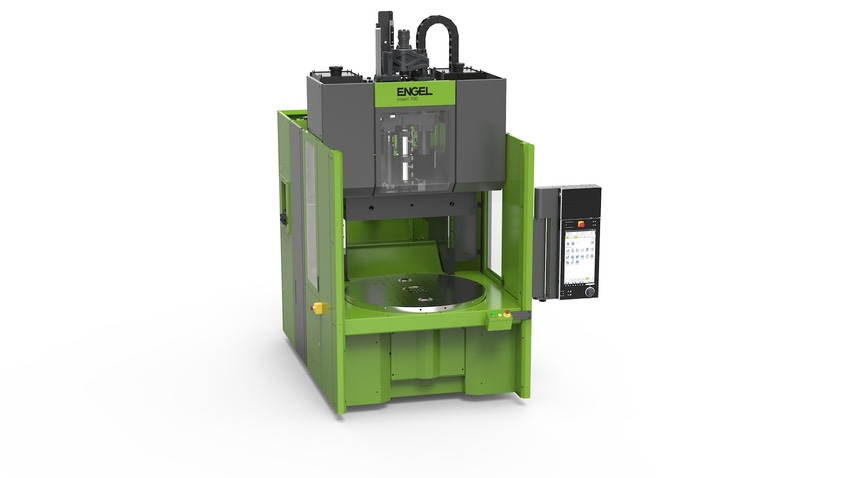
The global injection molding machine business has been struggling in recent times, with annual shipments down by as much as 40% year-on-year in some markets. Engel, whose financial year concluded at the end of March this year, didn’t suffer to the same extent, according to Gero Willmeroth, Asia president at Engel, with revenue down by just 6% to €1.6 billion ($1.7 billion). Standout performers were packaging in Europe and medical in the United States, while Willmeroth concedes that a weak auto sector in China and lackluster markets in Southeast Asia put a brake on sales in the Asian region.
Brand identity through illumination.
The automobile industry has always been an important market for Engel in China, and this was reflected in its presence at Chinaplas. Accompanying the transition from internal combustion engines to electric drives, the classic radiator grille has become obsolete as the main identity-creating element for automotive brands — this purpose is now increasingly being fulfilled by light.
The light guides required for this must be manufactured with great care and precision to ensure that no irregularities or impurities in the melt impair the required optical quality. For this application, the tie-bar-less Engel victory 120 plays to its strengths in combination with the optimelt process — internally developed and manufactured plasticizing components for acrylic (PMMA) resin enable gentle preparation of the melt and prevent yellowing and burn marks.
The tie-bar-less clamping unit enables precise molding of long and thin components thanks to its particularly homogeneous clamping force distribution. Engel says it is the machine of choice for the production of particularly long optical fibers with consistently high optical quality.
Another advantage: The tie-bar-less design means that even very large molds can be used on comparatively small injection molding machines. The exhibit on show is a victory machine with a clamping force of just 1,200 kN, whereas a tie-bar machine would reportedly require a significantly higher clamping force because of the space required for the mold.
Composite parts for the mobility of tomorrow.
A second highlighted application for the automotive sector is a vertical injection molding machine from the insert series. The insert 200V/100 rotary Pro machine is used to produce bipolar plates for fuel cells with a silicone seal in just one work step in a cycle time of 75 seconds with a 2.69-gram shot weight.
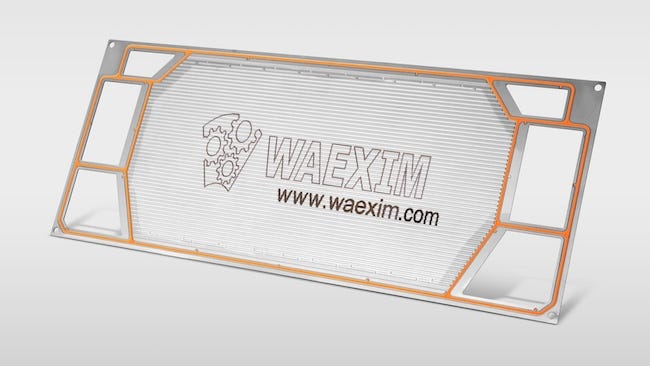
Bipolar plates for fuel cells are sealed with silicone in a single process. Image courtesy of Engel.
The particularly small footprint of the vertical machine and its ergonomic working area ensure efficient production of complex injection molded parts. Further, the precise servo-hydraulic drives of the insert simplify overmolding with complex geometries and the functionalization of components, even with materials that are difficult to process. The easily accessible mold area also enables the simple integration of upstream and downstream automation. In the application shown at Chinaplas, an Engel 6-axis robot handled the parts.
AI in injection, and more.
Engel’s Willmeroth also detailed some of the initiatives the company is working on in the realm of artificial intelligence (AI). The machine builder’s Process Observer software already uses AI, while the latest deployment is with a tool called Part Finder. In the past, Engel would often receive requests by telephone from processors asking for “the black part behind the pipe adjacent to the yellow part.” Now, the machine user only needs to take a photo of the part and forward it to Engel, who will use AI to identify the relevant item for shipping. “Critically, we have to explain to our customers and staff alike how to use AI [tools], or they won’t bother using them,” says Willmeroth. “The tools really need to be self-explanatory and able to be self-learned,” he emphasizes.
About the Author(s)
You May Also Like