Wittmann Battenfeld Debuts Energy-Efficient Press at Fakuma
New EcoPower B8X injection molding system features reduced energy consumption, short cycle times, and improved reproducibility.
August 22, 2023
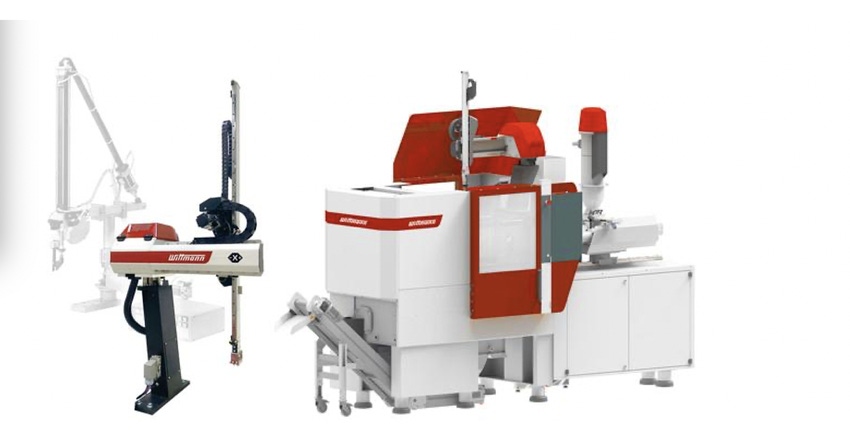
Wittmann Battenfeld is showcasing advances in energy-efficient injection molding at the international plastics processing tradeshow Fakuma in Friedrichshafen, Germany, from Oct. 17 to 21. The company notably will lay out an eight-station “energy efficiency path” in booth 1204 in hall B1. One of the highlights is the new EcoPower B8X injection molding system, which will make its debut at the event.
Reduced energy consumption
The EcoPower B8X offers several advantages in addition to a further reduction in energy consumption compared with previous systems. The new injection unit pivots, and lubrication is oil- rather than grease-based, reducing mechanical resistance. In combination with a range of additional injection unit sizes, this reportedly has a positive effect on the energy balance. The design of the toggle lever has been optimized in terms of dynamism and service life. The faster injection units in combination with the highly dynamic toggle lever enable extremely short cycle times, according to Wittmann Battenfeld.
The B8X control system comes with several system components developed in-house that enable a higher internal clock frequency, resulting in shorter response times to sensor signals and, thus, improved reproducibility.
Fakuma marks the debut of the EcoPower B8X on the European market in sizes ranging from 550 to 1800 kN.
The functionality of the new EcoPower B8X will be demonstrated at Fakuma on an EcoPower 110/350 B8X in combination with the new WX90 Wittmann sprue picker, designed as an Insider cell with integrated parts chute and S-Max screenless granulator, plus a WFC120 flow controller. The production cell will produce a bracket for a climbing net using an eight-cavity mold supplied by Austrian company Lechner. The sprue will be removed and transported directly to the integrated granulator by the WX90, which is also integrated in the B8X control system. Following grinding of the sprue, the material is fed back into the process.
Wittmann Battenfeld demos solar-powered systems
Solar cells on corporate roofs offer companies the possibility to generate their own electricity, saving money while protecting the environment. Wittmann Battenfeld has explored using direct current generated by solar cells to run injection molding equipment without first passing it through inverters.
At Fakuma, this technology will be demonstrated on an EcoPower 180/750+ B8X. With a single-cavity mold from Austrian company Kunststofftechnik Grabher GmbH, a drainage device will be manufactured from polypropylene. The part will be removed by a modified WX142 robot from Wittmann, which draws its power supply directly from the interim DC voltage circuit of the EcoPower and returns surplus energy to the interim circuit whenever the axes are delayed. To enable a live presentation of the DC technology to visitors, the machine will remain disconnected from the mains network of the exhibition hall during the fair and will be powered independently via a solar power storage battery supplied by Innovenergy. The battery has a total capacity of over 45 kWh, which is more than sufficient for continuous machine operation during an entire eight-hour day at the show.
But wait, there's more: Wittmann Battenfeld also will showcase the automated production of a bubble level and micro membrane for a high-end speaker at its booth. Read all about it.
About the Author(s)
You May Also Like